Key Features
- 1× CAN acc. to ISO 11898
- J1939 protocol support
- IP69K protection class
- Windspeed from 0–50 meter/s
- 360° wind direction
- Measurement of temperature and humidity
Description
The ultrasonic wind sensor convinces by an extremely compact and robust construction. The sensor has no moving parts and therefore no mechanical wear. All environmental data are measured and provided by ultrasonic technology. The data can be transmitted easily and quickly via one CAN interface and J1939 protocol support.
The sensor convinces with extremely fast data handling and can acquire up to 50 measurements per second. Wind speeds of 0–50 meters per second can be recorded. Further measurement data are wind direction, temperature and humidity. To prevent the sensor from freezing in sub-zero temperatures, the device also has an integrated heating system.
Technical Data
CAN | 1× CAN interface acc. to ISO 11898 |
Further protocols | J1939 |
IP classification | IP69K |
Wind directions | 0–360° |
Wind speed | 0–50 m/s |
Wind temperature | –40°C up to +70°C |
Humidity | 20 % – 80 %, temporarily 0 % – 100 % |
Air pressure | 300 hPa – 1200 hPa |
Heating | Yes |
Dimensions (l×w×h) | 100 mm × 133 mm × 71 mm |
Weight | app. 620 g |
Housing | Anodized aluminum |
Related Products
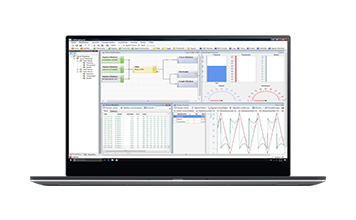
CANexplorer 4
Don’t lose any time during CAN bus diagnostics and benefit from the modular software for acquisition, processing, display and transmission of CAN data.
- Fieldbus analysis tool
- User-defined measurement setups
- Receive, process, send and abstract
- J1939 and CANopen protocol support

COMhawk® xt
Next generation embedded application ECU with up to four CAN interfaces. Use as telemetry and diagnostic module as well as gateway, data server and data logger.
- Powerful ARM Cortex-A9 processor
- 2× CAN acc. to ISO 11898 (opt. 4× CAN)
- 2G/LTE
- Linux operating system
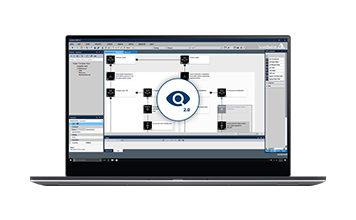
MDT® 2.0
Modular authoring system for the creation of complex diagnostic applications in the automotive sector. Based on ODX and OTX standard and an MCD-3D server.
- ODX support according to ISO 22901-1
- OTX support according to ISO 13209
- MCD-3D Server
- Platform independent