Key Features
- OPC UA Server and Client
- ODX acc. to ISO 22901-1
- OTX acc. to ISO 13209
- Multi platform support
- High-performance runtime system
Description
The new MDT® 2.0 provides a standardized tool to access data of the machine. It enables the standardization of data description (ODX), programming (OTX) and data sharing & provisioning (OPC UA).
OPC UA Standard
The manufacturer and platform independent architecture OPC UA enables access to machines and other systems.The obtained machine information can be transmitted to a supervisor and thus integrated or used in the entire environment.
ODX and OTX standard
The tool offers various options for the creation, structuring and implementation of test bench workflows based on the industry standard OTX (Open Test sequence eXchange) in accordance with ISO 13209, while the ODX standard (Open Diagnostic Data Exchange) guarantees the reusability of the service for test benches. In addition, MDT® 2.0 supports native RMI support and offers the innovative ODW Wizard (Sontheim OTX Diagnostic Wizard), which simplifies OTX editing in a very convenient way without breaching the ISO standard.
Multi platform support
The runtime was developed especially for multiplatform applications and offers GUI support as well as a platform-independent description of the runtime workflow description language. This reduces both the implementation and testing effort for your diagnostic applications across multiple PC, mobile or embedded platforms. The MDT® 2.0 allows you to create your diagnostic application once and run it on different environments such as Windows, Linux x86, Linux ARM or QNX without any customization.
Modern design
The MDT® 2.0 Authoring Tool is based on Visual Studio to meet the needs of modern developers. A new, clear and modern design allows the use of Visual Studio plug-ins for SVN, Git and other extensions commonly used for development. In addition, new graphical elements such as 2D and 3D animations can be used to create your diagnostic application, making diagnostics more visually appealing and more intuitive for service personnel and diagnostic users.
Technical Data
Minimum system requirements for the runtime system | Intel Pentium III, at least 750 MHz, at least 256 MB RAM, at least 800×600 resolution, USB 1.1 or higher |
Minimum system requirements for the development environment | Intel Pentium IV, 2 GHz or higher, 512 MB RAM |
Supported operating systems and hardware drivers | from Microsoft Windows 7 (32- and 64-bit) SP1 |
Supported CAN interfaces | COMfalcon®, COMhawk®, COMhawk® xt, CANUSB, CANfox®, CANUSBlight, PowerCAN-PCI V1 and V2, PowerCAN-PC104+, PowerCAN-PCI104 V2 |
General program structure | Graphical program flow editor for internal data flow of a diagnostics page surface editor |
Supported standards | OPC UA, ODX 2.2.1 to ISO 22901-1, OTX to ISO 13209, CANopen, SAE J2534, SAE J1939, ISO 15765 (KWP2000 on CAN), UDS, DoIP, others available on request |
Related Products
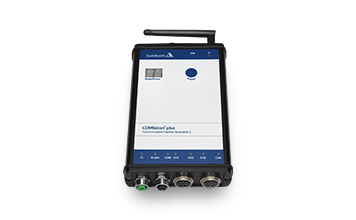
CAN interfaces
The CAN interfaces are all compact in design and offer USB, LAN and WLAN interfaces for connection to a service PC, laptop or tablet.
- Up to 6× CAN interface
- WLAN, LAN, Bluetooth, USB, ...
- LIN, RS232, RS485, ...
- With logging function
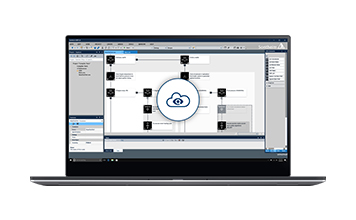
MDT® Service Cloud
The MDT® Service Cloud enables interactive data exchange of your diagnostic application at any time and from any location worldwide.
- Simple data exchange
- Administration of session logs, HEX files, etc.
- HTTPS logging & SSL/TLS encryption
- Direct ERP connection
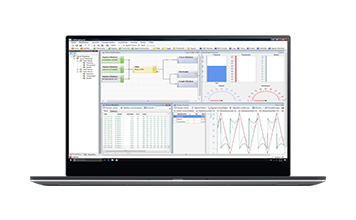
CANexplorer 4
Don’t lose any time during CAN bus diagnostics and benefit from the modular software for acquisition, processing, display and transmission of CAN data.
- Fieldbus analysis tool
- User-defined measurement setups
- Receive, process, send and abstract
- J1939 and CANopen protocol support