Key Features
- Own intelligence for self regulation and data management
- Safety features for high operating safety
- Free configuration and storage of operating data
- Compact housing with IP20 and integrated top hat rail mounting
Description
Functions of the channel
One motor can be controlled per channel. One encoder and one power supply per channel are available. Current limitation and current measurement can also be performed individually.
Safety is a top priority
The limit current is definable and is stored by the module as a base value, thus avoiding errors in the current calculation. The MC105 additionally has an emergency stop function, which is triggered in the absence of bus communication.
Technical Data
Hardware | |
---|---|
CPU | Philips Arm 7 |
Fieldbus | EtherCAT |
LEDs | 1× LED green for power supply 1× LED green for operation mode (Run) 1× LED red for error (Err) |
Display | 2 lines à 16 signs |
Dimensions (l×w×h) | 241 mm × 120 mm × 48 mm |
Weight | approx. 800 g |
Housing | Aluminium housing with protection class IP20 |
Storage temperature | –10°C up to +70°C |
Operating temperature | 0°C up to +60°C |
Rel. humidity | 90 % non-condensing |
Supply of the motors | Isolated, 24 V DC up to max. 5 A |
Power supply | 24 V DC |
Related Products
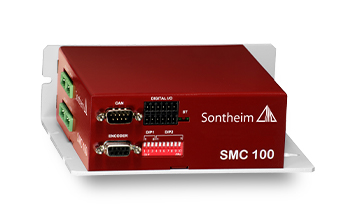
SMC 100
The stepper motor controller controls bipolar 2-phase stepper motors with high precision.
- Phase current of up to 10 A
- 4 galv. isolated in- and outputs each
- 1× CAN interface acc. to ISO 11898
- Own intelligence for self-regulation and data management