Key Features
- OPC UA ready
- EtherCAT and CAN compatible
- Modular Diagnostic Toolchain MDT 2.0 can be integrated
- Linux operating system
Description
Features and display
The IMX6 Quad Core processor has a 1 GB working memory and the possibility to expand the memory with an SD card slot. With the help of the resistive touch screen, data can be intuitively visualized and software components operated. The modular econtrol mIO xt is therefore ideally suited as an HMI for machine control.
Variety of interfaces
The HMI is equipped with a number of interfaces. In addition to a motion sensor, the controller has two CAN, Ethernet and USB connections each and up to six temperature sensor inputs. An interface board carries the digital inputs and outputs, as well as the majority of analog interfaces. All connectors are accessible from the rear panel.
Unbeatable team: MDT 2.0 integration
On the HMI, the Modular Diagnostic Toolchain can be integrated with OPC UA, creating the perfect state-of-the-art solution for your Industry 4.0 applications. The new MDT® 2.0 provides a standardized tool to access data of the machine. It enables the standardization of data description (ODX), programming (OTX) and data sharing & provision (OPC UA). It is the perfect basis for innovative machine park monitoring. Combined with the HMI, Sontheim creates the all-round package: smooth machine control, standardized diagnostics and simple cloud connection.
Motion sensor
A motion sensor is integrated as part of the front panel. The pyroelectric sensor, or PIR sensor for short (Passive Infraed Sensor), reacts to motion and turns on the display and backlight as soon as motion is registered. This function is used to turn off the display and backlight when the device is not being operated and saves energy.
Technical Data
Hardware | |
---|---|
CPU | IMX6 Quad Core |
Co-Processors | 2× ATXMEGA, 1× LPC433x |
RAM | 1 GB LPDDR2 |
Memory | 4 GB |
Display | 10.1" RGB 1280 (W) ×3(RGB) ×800(H)dots / 500cd / IPS / anti-glare |
Touch | resistive |
LEDs | 2 LEDs for display of power supply and CAN communication |
Dimensions (l×w×h) | 300 mm × 200 mm × 55 mm |
Storage temperature | –25°C up to +85°C |
Operating temperature | 0°C up to +60°C |
Real-time clock | 2 weeks buffered via supercaps |
Weight | approx. 2.1 kg |
Protection class (front) | IP65 |
Protection class (back) | IP20 |
Power supply | 24 V DC ±15 % |
Interfaces | |
---|---|
Motion sensor | 1× PIR sensor |
CAN | 2× CAN interface acc. to ISO 11898, galv. isolated |
USB | 2× USB 2.0 |
Ethernet | 2× (1× 100 Mbit/s: EtherCat, OPC UA; 1× 1000 Mbit/s) |
Digital inputs | 24× DI (3×8), 24 V DC |
Digital outputs | 24× DO (3×8), 24 V DC |
Analog inputs (optional) | 10× AI, 16 bit, Output voltage range: 0 up to10 V Output current range: 0 up to 20 mA |
Analog outputs (optional) | 4× AO, 16 bit Output voltage range: 0 up to 10 V |
Temperature sensor inputs | 4× 24 bit, optional up to 6× |
SD card slot | 1× |
Operating system | |
---|---|
Operating system | Linux |
Related products
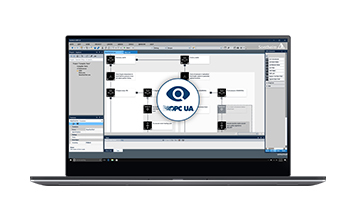
MDT® 2.0 with OPC UA
Next generation modular diagnostic tool for innovative machine park monitoring. Based on OPC UA, ODX and OTX standards.
- OPC UA Server & Client
- ODX 2.2.1 according to ISO 22901-1
- OTX according to ISO 13209
- Multi platform support
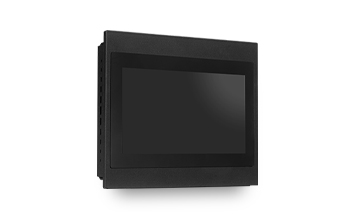
eControl mIO
PLC control with numerous communication interfaces and the possibility to control stepper motors
- 7" Touch display
- Numerous IOs, like stepper motor interfaces
- Integrated microSD slot up to 64 GB
- Optional: WLAN, Bluetooth
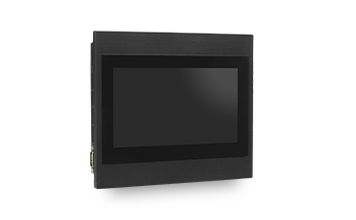
eControl micro II
PLC control with OPC UA server, IO-Link for IoT applications can be used manufacturer and platform independent.
- 7" Touch display
- OPC UA server, IO link
- Codesys V3.5 accord. to IEC 61131-3
- CAN and EtherCAT interface