Key Features
- 1 or 2 galv. isolated CAN interfaces with 1 Mbit/s transfer capacity at 90 % bus load
- Hot plug and play ensures fast and convenient commissioning
- MT-API enables access to CAN bus for own applications
- Optional variant with error frame detection
- Ideal for use with a PC or notebook
- Shock-resistant aluminium extrusion housing
Description
Hosuing
The interface is made of an extruded aluminium housing. Due to its compact design and high shock resistance it is used very successfully in various areas of the automation and automotive industry.
CAN channels
It has either one or two galvanically isolated CAN channels according to ISO 11898-2 with a transfer rate of 1 Mbit/s at 90 % bus load. The CAN interfaces are each galvanically isolated and are implemented via a 7-pin round connector.
More flexibility in data acquisition
With the USB 2.0 interface, the CANUSB can be operated on any notebook and desktop PC. The hot plug and play system makes its use even faster and more efficient, so that it can be put into operation quickly and without restarting the PC.
Microcontroller and firmware update
The STAR12 from Motorola and the PDIUSBD12 from Philips guarantee fast data processing. Both CAN 2.0 A and CAN 2.0 B are supported.
A firmware update is done directly via the USB interface.
Error frame detection
With this optional feature the CANUSB is able to take over debugging and diagnosis in a CAN network. The interface has its own logic which detects error frames and counts them in an internal memory. This allows sporadic errors, such as the corruption of messages by a participant in the network, to be detected.
Level mesasurement
This feature makes it possible to read in the CAN levels analogously and thus, for example, to carry out fault diagnosis on a vehicle or machine. It is especially important when data is lost from the network, which can be caused by short circuits, for example.
Programming interface
With the CANapi it is possible to access the CAN bus for an own application. The SiECA132 MT-CANapi with four simultaneous handles is provided as standard.
Technical Data
CPU CAN | Motorola Star12, 16-bit |
CPU USB | Philips PDIUSB12 |
CAN | 1× CAN interface acc. to ISO 11898-2, galv. isolated (optional 2× CAN) |
CAN Connections | 1× 7-pin round plug |
USB | 1× USB 2.0 |
USB ports | 1× standard USB connector type A |
Cable CAN | optional 2 m CANUSB cable |
Cable USB | 1 m Standard USB |
Max. data transfer | 1 Mbit/s at 90 % bus load |
Error frame detection | optional |
Analog level measurement | integrated |
LEDs | 2× triple 3 mm LED angled |
Dimensions (l×w×h) | 100 mm × 57 mm × 32 mm |
Weight | 166 g |
Housing | Solid aluminium |
Operating temperature range | 0°C up to +70°C |
Storage temperature range | –20°C up to +85°C |
Rel. Humidity | 20 % – 90 % non-condensing |
Power consumption | max. 350 mA at 5 V |
Power supply | via USB interface |
Related Products
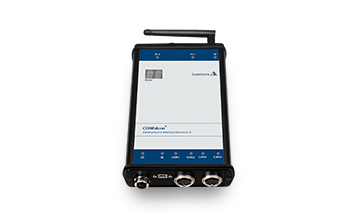
COMfalcon®
Powerful CAN interface with WLAN/LAN connection for recording CAN data and monitoring entire networks.
- RS 232, RS 422, RS 485, K-Line
- Protocolhandling
- Compact housing with protection class IP65
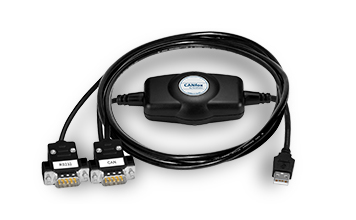
CANfox®
Compact CAN interface with each one CAN- and RS232 interface.
- Connection via USB 2.0
- Free configuration of the baud rate including 800 Kbit/s
- Multi-Thread API for own applications
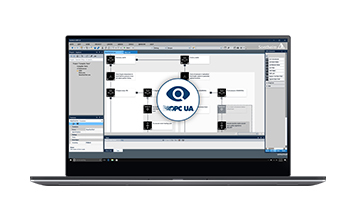
MDT® 2.0 with OPC UA
Next generation modular diagnostic tool for innovative machine park monitoring. Based on OPC UA, ODX and OTX standards.
- OPC UA Server & Client
- ODX 2.2.1 according to ISO 22901-1
- OTX according to ISO 13209
- Multi platform support